Bulletin – March 2012 India's Steel Industry
- Download the article 161KB
Abstract
Indian steel production has grown strongly in recent decades and India is now the world's fourth-largest steel producer. Nevertheless, India's consumption of steel relative to the size of its economy is very low by international standards. As the economy develops further, steel consumption is likely to increase. Indeed, Indian steelmakers have plans to expand capacity substantially in order to meet the anticipated increase in demand. While India has relatively large reserves of iron ore, its steelmakers import most of the coking coal they require. As Australia is a major supplier of coking coal to India, these exports from Australia are likely to expand further.
Introduction
Steel production in India has expanded rapidly in recent decades and, as a result, India has become the world's fourth-largest producer of crude steel (having been the 10th largest in 1995; Graph 1). Relative to the size of its economy, India's steel consumption, however, remains low; with large additions to steelmaking capacity planned to meet expected growth in steel demand, the nation's steel industry is expected to expand as India develops further.
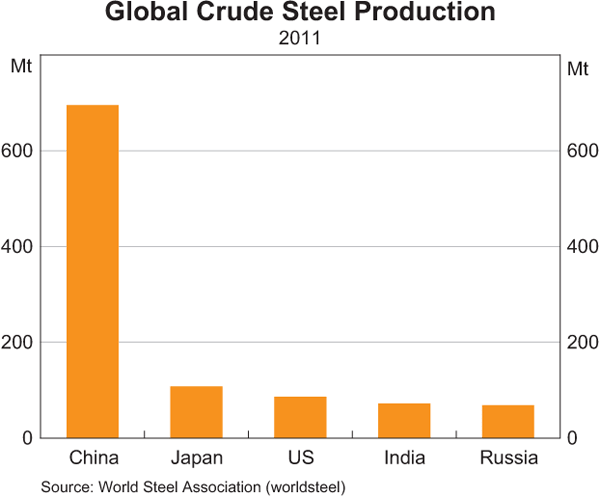
While India has large reserves of relatively high-quality iron ore, its reserves of coking coal are limited and mostly unsuitable for steelmaking; accordingly, Indian steelmakers import much of the coal required for producing steel. Australia is a major source of India's coking coal imports, and given its proximity to India, these exports are likely to grow as Indian steel production expands. This article discusses the Indian steel industry, focusing on its structure, the production technologies used and the sources of its steelmaking commodities.
History and Structure
Prior to independence in 1947, India had a small steel industry comprised entirely of private sector firms. India's first Five Year Plan, introduced in 1952, imposed a number of restrictions and effectively placed the sector under state control. Large-scale expansions in steelmaking capacity were reserved for public sector enterprises, the Indian Government set the price of steel sold by large producers and quantitative restrictions and tariffs were imposed on imports of inputs and finished steel. Sizeable public sector investment in steelmaking capacity since the first Five Year Plan helped steel production grow strongly in the decades following independence, with average annual growth exceeding 8 per cent between 1950 and 1970 (Joint Plant Committee nd).
Steel production continued to expand during the 1970s and 1980s, though slowed somewhat from the pace of the preceding decades, consistent with lower rates of growth in per capita incomes over this period (Baker and Cagliarini 2010). A new industrial policy introduced in the wake of the early 1990s balance of payments crisis removed many of the restrictions on the steel industry and tariff barriers were reduced; furthermore, foreign investment in the sector was permitted, with the steel industry included on the list of ‘high priority’ industries for automatic approval of up to 51 per cent foreign equity investment. Private sector firms, in particular, took advantage of their ability to expand, and steel production accelerated. Growth in steel production in the 1990s averaged around 10 per cent (Graph 2).
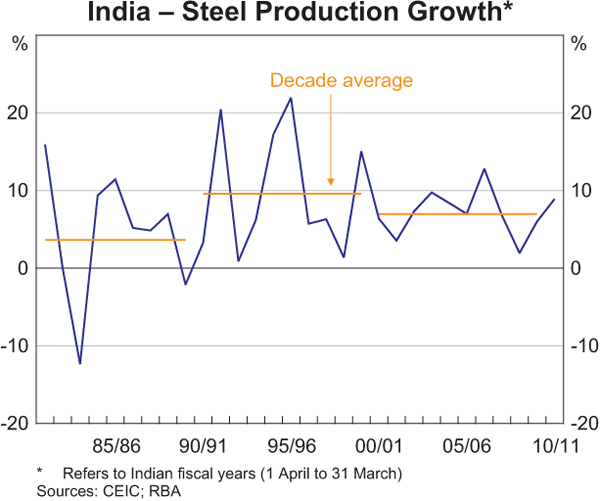
The sector continued to expand at a relatively rapid pace in the early 2000s, and the government announced India's first National Steel Policy in November 2005 to guide the future development and growth of the sector. The policy's stated long-term goal was that ‘India should have a modern and efficient steel industry of world standard, catering to diversified steel demand’ (Ministry of Steel 2005). The policy projected that India's domestic steel production would grow in line with GDP to reach 100 million tonnes by 2019/20.[1] However, more recent estimates suggest that India's steelmaking capacity will exceed 100 million tonnes by as early as 2013 (Ministry of Steel 2011).
The legacy of earlier public sector involvement is reflected in the current structure of the Indian steel industry, with the state-owned Steel Authority of India Limited and Rashtriya Ispat Nigam Limited still accounting for around a quarter of total crude steel production in 2009/10 (Ministry of Steel 2011). Including the two largest private steelmakers, TATA Steel and JSW Steel, these producers operate a handful of integrated steel plants that account for the majority of steel made in India using the blast furnace/basic oxygen converter method (Table 1). This method of steelmaking uses coking coal and iron ore as primary inputs, though scrap steel can be substituted for iron ore.
Process | Number of plants | Production | Production |
---|---|---|---|
Megatonnes | Share of total (%) | ||
Blast furnace/basic oxygen converter | 13(a) | 29 | 45 |
Electric arc furnace | 39 | 16 | 24 |
Electric induction furnace | 1,114 | 20 | 31 |
Total | na | 65 | 100 |
(a) Refers to the number of integrated steel plants with at least one blast furnace; some plants have multiple blast furnaces or a combination of both blast and electric furnaces Sources: Ministry of Steel (2011); authors' calculations; company websites |
Private firms dominate the production of steel using the two electric furnace methods; three large producers account for roughly half of all electric arc furnace steelmaking, while electric induction furnace steelmaking is very decentralised, with over a thousand plants operating in 2009/10 (Table 1). Electric furnace steelmaking can utilise both scrap steel and direct-reduced iron – made from iron ore – as inputs, without requiring the addition of coking coal.[2]
Strong growth in private sector steelmaking, which tends to use smaller capacity plants, together with broadly stable public sector capacity means that the electric furnace methods now account for the majority of India's steel production. As a result, steelmaking in India is less commodity intensive than elsewhere; the share of crude steel produced using the blast furnace/basic oxygen converter method in India is half that of China and the lowest among the major steel-producing countries (World Steel Association 2011). Even so, much of the steel produced by electric furnaces in India uses direct-reduced iron rather than scrap metal, so iron ore is still used as an input for most of the crude steel produced in India.[3]
Steel Demand and Trade
The production of finished steel in India is fairly evenly split between ‘long products’ (bars, rods, wires, etc), which are typically used in construction, and ‘flat products’ (steel strips, plates, sheets, etc), which are used in manufacturing. Construction and infrastructure are estimated to account for roughly 40 per cent of steel consumption, and manufacturing (including automobile production) for around 30 per cent of consumption (Indicus Analytics 2009).
While domestic steel production has historically been sufficient to satisfy domestic demand, India has recently become a net importer of steel, reflecting strong growth in Indian steel consumption (Graph 3). Imports of flat products have grown particularly strongly in recent years, as manufacturing production grew strongly in the years leading up to the global financial crisis and has recovered strongly subsequently. At the same time, India's steel exports have fallen (with the exception of shipments of pipes and tubes). Nonetheless, steel remains an important source of export revenue, accounting for around 4 per cent of the total value of India's exports in 2010.
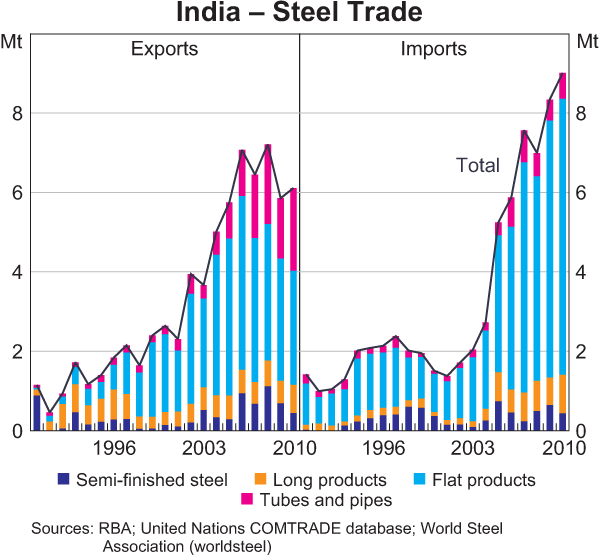
Most of India's imports of steel come from other large steel-producing countries. Imports from China have grown strongly over the past five years or so, with China now accounting for around one-third of the value of India's steel imports (Table 2). Sizeable steel imports from advanced economies suggest that there are certain types of products that are either not produced in India or for which domestic capacity is insufficient to meet demand; for example, Indian automakers import much of the high-grade steel used for manufacturing outer panels of cars (Mazumdar 2010). While the United States is the largest destination for Indian steel exports, around one-third of exports go to oil-producing countries in the Middle East (Table 2). Detailed export data reveal that a large share of the shipments to the Middle East consists of steel pipes suitable for oil and gas pipelines. India was the world's largest exporter of steel pipes for oil and gas pipelines in 2010, and lower shipping costs (owing to the relative proximity of India to the Middle East) are reflected in the region's oil-producing countries sourcing the majority of their imports of pipelines from India.
Exports | Imports | |||||||||
---|---|---|---|---|---|---|---|---|---|---|
2010 | 2000 | 2010 | 2000 | |||||||
Destination | Share of total(a) | Destination | Share of total(a) | Origin | Share of total(b) | Origin | Share of total(b) | |||
United States | 14.0 | United States | 28.3 | China | 29.8 | Japan | 15.8 | |||
Saudi Arabia | 9.4 | United Arab Emirates | 6.6 | South Korea | 13.9 | Russia | 13.9 | |||
United Arab Emirates | 7.9 | Italy | 5.8 | Japan | 11.7 | Germany | 9.4 | |||
Belgium | 7.7 | Canada | 5.6 | Russia | 5.3 | South Korea | 8.9 | |||
Iran | 7.0 | Sri Lanka | 4.2 | Germany | 4.9 | Ukraine | 7.2 | |||
(a)Share of the total value of India's steel exports Source: United Nations COMTRADE database |
Consistent with India's low income per capita, its steel consumption per capita is currently very low relative to other large economies. In 2010, India's consumption of steel (in crude steel equivalent terms) was 49 kg per capita, compared with 539 kg in Japan, 445 kg in China, 292 kg in the United States and a world average of around 220 kg (World Steel Association 2011). India's low steel consumption partly reflects its relatively limited urbanisation to date; in 2010, only 30 per cent of India's population lived in urban areas (compared with an average of 42 per cent across Asia) having risen from under 20 per cent in 1970 (United Nations 2010). The pattern of development in other major economies suggests that India's steel consumption per capita will continue to grow, although the speed of this increase will largely be determined by the rate at which India urbanises and industrialises (Graph 4).
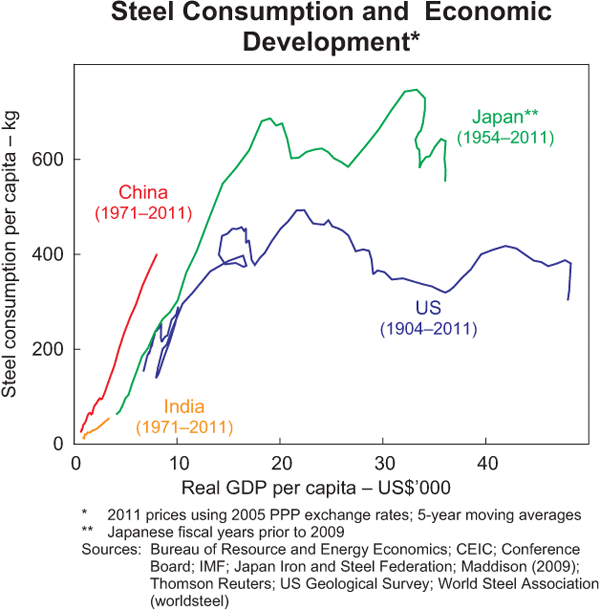
To cater for increases in domestic steel demand, the Indian steel industry has expansion plans which, if fully realised, would see capacity expand to over 275 million tonnes – a more than threefold increase in capacity (Ministry of Steel 2011). As much as 30 million tonnes of additional capacity is expected to come online during 2011/12 and 2012/13, which should see productive capacity increase by roughly 40 per cent. The Indian authorities are also optimistic about the medium-term prospects for steel production, with the Ministry of Steel (2011) expecting that India will overtake Japan and the United States to become the world's second-largest producer of crude steel by 2015/16.
Demand for Iron Ore and Coking Coal
India's demand for iron ore is currently met largely through extraction of high-quality hematite reserves located in the eastern states of Odisha, Jharkhand and Chhattisgarh and the south-western states of Karnataka and Goa. Extraction and crushing of the iron ore processed from these reserves leaves it in the form of lumps (56 per cent of iron ore), fines (21 per cent), and a mix of lumps and fines (13 per cent).[4] Lumps are ready for use in steel production, whereas fines are smaller in size and are required to go through an agglomeration process (typically either sintering or pelletisation) before they can be used in steel production.[5] Additional domestic demand is met by the country's deposits of lower grade magnetite reserves, extracted as fines (Indian Bureau of Mines 2011a).
India is currently the world's third-largest exporter of iron ore behind Australia and Brazil. In recent years, however, India's exports as a share of total production have been declining (World Steel Association 2011). Shipments to China, which account for over 85 per cent of Indian exports of iron ore, have fallen over the past few years, even as China's demand for imported iron ore has grown (Graph 5). Part of this decline in exports is attributable to the desire of policymakers to make more use of India's iron reserves for domestic steel production, which has been actively pursued through the use of export duties on iron ore. Through 2009 and 2010, export duties were raised from 0 to 5 per cent on fines, and from 5 to 15 per cent on lumps. Duties for both were raised to 20 per cent in the 2011/12 budget, and then again to 30 per cent at the beginning of 2012. These higher duties are reducing India's contribution to the seaborne iron ore market and shifting demand for iron ore to other major exporters such as Australia and Brazil.
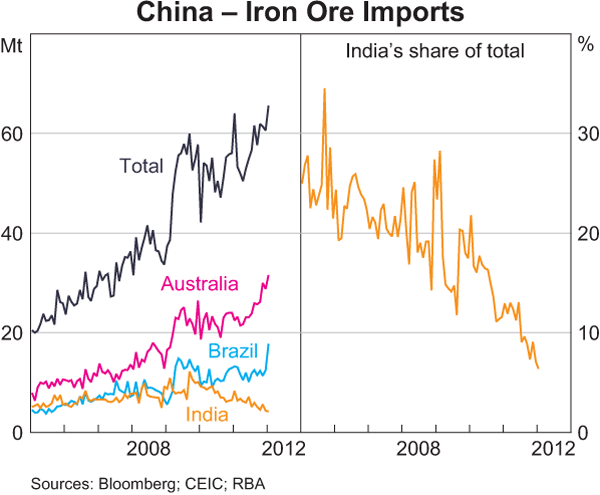
Indian policymakers are also seeking to increase domestic agglomeration of iron ore fines, which will further limit India's contribution to the seaborne market. In 2009/10, 90 per cent of Indian iron ore exports were in the form of fines (equivalent to over 70 per cent of total fines production). As agglomeration procedures are capital intensive to start up, the bulk of these facilities in India are operated by integrated steel plants. India's iron ore industry has many participants (319 reported mines in 2009/10), but is highly concentrated, with 18 per cent of mines producing 72 per cent of total output (Indian Bureau of Mines 2011a). The National Steel Policy has recognised the need to increase agglomeration capacity and encourage the formation of consortiums among smaller mines in order to pool their fines and make greater use of this resource domestically (Indian Bureau of Mines 2011b).
Over the next 15 to 20 years, existing high-grade hematite reserves are expected to be depleted (Indian Bureau of Mines 2011b). However, India expects to remain self-sufficient in its supply of iron ore for the foreseeable future. Advances in drilling technology are expected to allow access to more reserves beyond the current attainable depth in iron ore mining areas. Additionally, exploration in some known hematite-bearing regions has not been exhaustive; as this exploration continues, estimates of hematite reserves are expected to increase. Furthermore, greater domestic consumption of fines and the restriction of supply to the global market will help to ensure a sufficient supply of local resources.
By contrast, Indian coking coal reserves are quite small and tend to be of low quality, needing to be blended with higher-grade imported coal for use in steel production. To meet rising demand from steel production, India has become an increasingly large purchaser in the global coking coal market. India is now the third-largest importer of coking coal in the world (World Coal Association 2011). Since the early 2000s, Australia's coking coal exports to India have risen steadily, and India is now the second most important destination of these exports behind Japan (Graph 6). Coal now comprises around one-third of the value of Australian exports to India, with almost all of coal exports made up of coking coal.
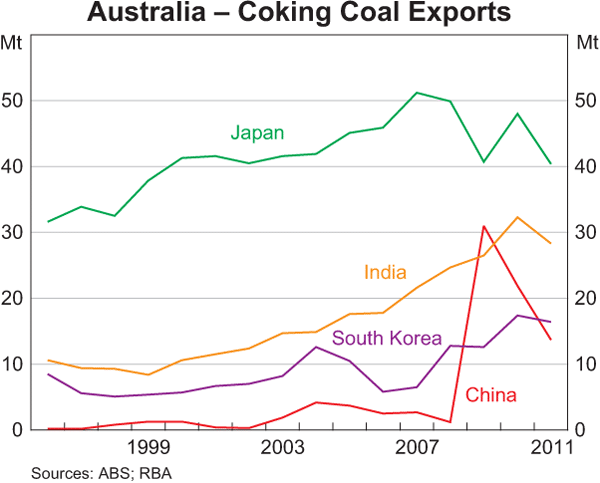
India's National Steel Policy has identified the need to further develop non-coking coal methods of steel production, such as the use of electric arc furnaces (Ministry of Steel 2005). However, given existing blast furnace production capacity, this technology is likely to continue to play a role in the development of the local steel industry and drive further demand for Australian coking coal in the future.
Conclusion
Indian steel production has grown strongly in recent decades and is likely to continue to expand as domestic producers increase their capacity to meet anticipated demand. Given its relatively large reserves of iron ore, India is likely to remain self-sufficient in its supply of iron ore for the foreseeable future. In contrast, Indian steelmakers rely heavily on imports for their coking coal needs. As Australia is a major supplier of coking coal to India, growth in Indian steel production is likely to see these exports from Australia expand further.
Footnotes
The authors are from Economic Group. [*]
All mentions of fiscal years in this article refer to Indian fiscal years, which run from 1 April to 31 March. [1]
Direct-reduced iron is made by reducing iron ore to iron by heating it in the presence of gas containing hydrogen and carbon monoxide. It is also known as sponge iron. [2]
The Ministry of Steel (2011) estimates that steel generated from ship recycling accounts for 1 to 2 per cent of total Indian steel demand. Furthermore, imports of steel scrap were equal to around 7 per cent of the production of finished steel in 2009/10. These figures suggest that scrap is used as an input for at least 8 per cent of the finished steel produced in India, though the actual figure is likely to be higher once other sources of scrap, such as the recycling of durable goods, are taken into account. [3]
The remaining 10 per cent are processed as black iron ore, other or unknown grades. [4]
Iron ore fines cannot be used directly in blast furnaces as they block the flow of air around the raw materials. Agglomeration is the process of converting fines into lumpier aggregates, either with or without additives such as limestone or dolomite. Sinters are made of coarser iron ore fines and are the preferred input in blast furnaces, whereas pellets are made from very fine iron ore. [5]
References
Baker M and Cagliarini A (2010), ‘Economic Change in India’, RBA Bulletin, September, pp 19–24.
Indian Bureau of Mines (2011a), ‘Indian Minerals Yearbook 2010’. Available at <http://ibm.nic.in/imyb2010.htm>.
Indian Bureau of Mines (2011b), ‘Iron & Steel – Vision 2020’. Available at <http://ibm.nic.in/vision2020.htm>.
Indicus Analytics (2009), ‘Indian Steel Industry: Final Report Prepared for the Competition Commission of India’, January. Available at <http://www.cci.gov.in/images/media/completed/Indicussteel_20090420151842.pdf>.
Joint Plant Committee (nd), ‘Steel Frame: Profile of the Indian Iron and Steel Industry’. Available at <http://jpcindiansteel.nic.in/profile.asp>.
Maddison A (2009), ‘Statistics on World Population, GDP and Per Capita GDP, 1-2008 AD’. Available at <http://www.ggdc.net/MADDISON/Historical_Statistics/horizontal-file_02-2010.xls>.
Mazumdar R (2010), ‘Emerging Hub for Automotive Steel’, www.economictimes.com, 28 May. Available at <http://articles.economictimes.indiatimes.com/2010-05-28/news/27593564_1_nippon-steel-auto-steel-automotive-steel>.
Ministry of Steel (Ministry of Steel, Government of India) (2005), ‘National Steel Policy – 2005’, November. Available at <http://steel.nic.in/nspolicy2005.pdf>.
Ministry of Steel (2011), Annual Report 2010–11. Available at <http://steel.nic.in/Annual%20Report%20(2010-11)/English/Annual%20Report%20(2010-11).pdf>.
United Nations (United Nations Department of Economic and Social Affairs/Population Division) (2010), World Urbanization Prospects: The 2009 Revision, United Nations, New York.
World Coal Association (2011), ‘Coal & Steel Facts 2011’, August. Available at <http://www.worldcoal.org/bin/pdf/original_pdf_file/coal_and_steel_facts_2011(17_08_2011).pdf>.
World Steel Association (2011), Steel Statistical Yearbook 2011, World Steel Association, Brussels, pp 24–25. Available at <http://www.worldsteel.org/dms/internetDocumentList/yearbook-archive/Steel-statistical-yearbook-2011/document/Steel%20statistical%20yearbook%202011.pdf>.